蒸汽的膨胀性系数影响孔板蒸汽流量计测量结果
流量计通常针对稳定工况条件设计,当运行工况为非稳定状态时,其测量精度会受到较大影响。针对非稳定运行的工作条件,分析了影响孔板式蒸汽流量计测量的各项因素。通过对稳定测量条件下的计算公式进行修正,获得非稳态条件下的计算公式,并通过实验方式进行质量平衡标定。结果表明: 当实际运行工况与设计参数发生偏离时,蒸汽的膨胀性系数会偏离设计值,进而影响测量结果。修正后的流量计,可以适用于非稳定条件下的蒸汽测量,计算精度有了明显提高。水蒸气是工业生产过程中使用的重要介质,许多蒸汽流量计的使用和分析人员对蒸汽流量的准确计量进行了研究,并积累了一些经验 。目前*常用的蒸汽流量计为差压式流量计和涡街流量计,并配以蒸汽密度补偿。而蒸汽密度补偿一般采用蒸汽压力、温度补偿的方法,分别由安装在管道上的压力变送器和温度变送器来实现 。通常工业使用蒸汽流量测量用于稳态测量,工作状态变化较小,流量计的设计状态与实际使用状态差别较小,若按照正确合理的方式选择、安装流量计,并进行温度压力补偿,则基本可以满足测量要求。
然而对于利用蒸汽进行的实验过程,很多情况下要求在不同工作条件下进行工作,工作状态跨度较大,且经常需要瞬态测量。例如: 在缩比例模拟核电站大破口状态下蒸汽喷放整个质能释放过程时,流量要求可能在1~100t/h范围内变化。这种跨度很大的蒸汽流量测量,在实现时会通过几条支路分别供应,但也只能分成有限的大小支路提供,难以满足蒸汽流动参数**变化条件下的蒸汽流量测量。本文从孔板式流量计基本计算公式出发,分析公式中各参数对变状态流量测量的影响,结合实验数据,拟合获得能够适应变工况参数的蒸汽流量测量公式,提高蒸汽流量在不稳定状态条件下的测量精度。
1、孔板质量流量计计算公式
1.1理论计算公式
差压式流量计的理论依据是伯努利方程和流动连续性方程。当流体流经节流装置,部分压力能转换为动能,同时产生差压信号。该差压值与流量的平方成正比,其数学模型对于孔板式差压流量计质量流量基本计算公式为:
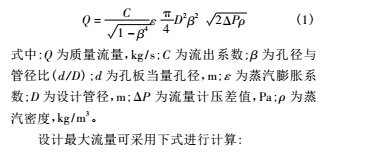
2、测量影响因素分析
影响质量流量计测量结果的因素有很多,包括孔板结构、取压形式及孔位置、流量计安装、工作介质、差压表精度以及工作状态对应的流体物性参数等。本文主要针对稳态测量和非稳态测量工作状态可能造成差异的几个因素进行分析,如流出系数、膨胀性系数、蒸汽温度、压力及流量等。
2.1流出系数
流出系数主要受孔板结构即孔径比β和雷诺数影响。对于特定流量计β基本不变。孔板流量计流出系数与雷诺数的关系如图1所示。
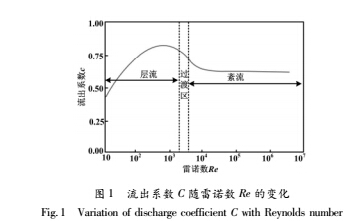
由图1可见,在低、中雷诺数时,C值随雷诺数而变化,而在高雷诺数(大于10000,紊流区)区域,C值变化较小。本文设计的流量计根据出厂报告可知实际工况均远大于10000,所以实验工况基本处在紊流区,不同工况下流出系数变化较小。
2.2膨胀系数
膨胀系数是对流出系数在可压缩性流体中密度变化的修正。对于孔板流量计,由于流量计膨胀既是轴向的又是径向的,目前主要按照经验公式计算。按照ISO5167,孔板的三种取压方式采用同一可膨胀性系数公式,适用于空气、蒸汽及天然气等介质,如下式所示。

式中:β为孔径与管径比,是结构相关参数,正常使用时可认为不变;k为物性参数,跟工质有关。
因此,膨胀系数大小主要受孔板上下游的压力影响。设计*大流量时膨胀系数为*大流量下的对应值。如在0.8MPa(表压)、流量10t/h时膨胀系数约为0.88左右。实际蒸汽喷放时,如果工作上下游压力没有处在稳定状态时,运行工况偏离设计工况,实际膨胀系数与设计膨胀系数不符,从而影响流量测量。
2.3工作压力、温度影响
当进行稳态流量计设计时,流量计的工作压力基本恒定,给定工作压力和流量下均有对应的膨胀性系数,而在瞬态测试或者背压变化较大时工作压力会发生较大变化。不同温度和工作压力下膨胀性系数的数值如表1所示。本文设计实验条件背压可能会从0( 表压)逐渐增加至约1.0MPa(随背压变化而变化)。
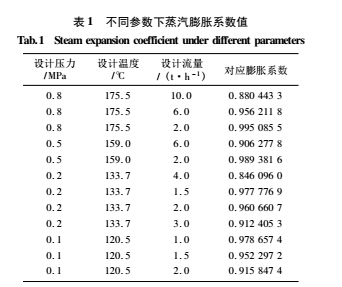
从表1给出的膨胀系数数值可以看出,相同流量下,工作温度和压力越低,膨胀系数越小。
2.4流量影响
如表1所示,在相同工作压力下,流量越小,相应的膨胀系数越大,即更接近于1。在非稳定瞬态测量时,温度压力直接的作用可通过测得的温度及压力数值进行温压补偿处理,不会影响瞬态测量。当对于蒸汽工质,温度和压力的变化会影响综合压力和流量对膨胀系数的作用。以蒸汽1.5t/h喷放为例,工作压力0.1MPa时为0.9523;0.2MPa时为0.9778。0.5MPa下、流量2t/h时,膨胀系数为0.9894。当流量上升到6t/h时,膨胀系数降为0.9063,相差10%左右。整个实验过程实验工作压力从0变化为0.8MPa左右。如果采用固定的膨胀系数计算质量流量会导致10%以上的计算误差。
3、流量计测量修正方案
依据上述分析,对于蒸汽质量流量计,目前流量计测量主要误差主要源于膨胀系数的偏离。水蒸气膨胀系数ε常用计算公式为:

式中:P1、P2分别为流量计上游压力及下游压*低点的压力。
尝试采用流量计采集的差压信号作为(P1-P2)的压差带入计算后发现ε数值变化很小,基本接近于1,而这与流量计设计计算给出的ε也相差较大。从压力定义看,P2为孔板下游流速*大、压力*低点的压力值,这与流量计取压孔获取压力有一定的区别。这里在取信流量计设计提供的ε的基础上,利用设计提供的不同条件下的ε值拟合出P2与流量计差压信号的关系,结果如下:

4、实验系统及实验结果分析比较
4.1实验系统
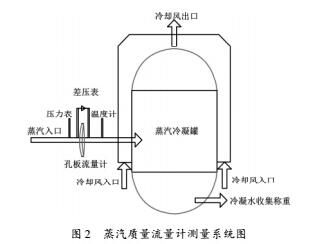
蒸汽流量计使用的系统图如图2所示,图2中蒸汽经过孔板质量流量计后进入罐体,罐体外表面有环形通风,可用于冷却罐体。流量计前后布置有温度、压力补偿测点,同时将流量计的实时测量结果进行采集汇总。蒸汽进入罐体后会提升关内压力,同时会在罐内冷凝,冷凝的热量通过罐外部冷却带走。进入罐内的蒸汽完全冷却后可由下部出口将冷凝水排出称重,将称重结果与流量计实时测量结果进行对比,以验证质量流量计变工况测量准确性。实验过程中,随着蒸汽进入罐体,罐内蒸汽难以及时完全冷凝,压力会逐渐上升,这会导致上游流量计附近蒸汽状态也会随之变化,即流量计工作状态与设计值相比在不断变化,这种变化会随着蒸汽流量的增大而逐渐增大。
4.2实验结果比较分析
通过实验获得蒸汽流动过程中测得的各项参数,并使用通用公式及修正后的公式进行相应计算处理,获得所需数据。如图3所示为修正前后膨胀性系数**间变化的关系。
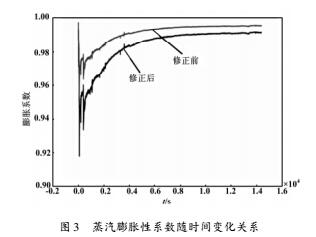
从图3可以看出,随着时间的变化,膨胀性系数逐渐增大,6000s后流量计工作状态保持稳定,膨胀性系数基本保持不变。比较修正前后的膨胀性系数,修正后的膨胀性系数明显小于修正前,与表1中数值更加接近。对膨胀性系数修正的结果可以代入式(1)中进行相应的蒸汽质量流量计算,结果如图4所示。在经历了一小段增长段后,质量流量基本保持稳定,变化很小。相比于膨胀系数的逐渐减小过程,修正前后的孔板流量差距在整个过程中保持稳中有升的状态。
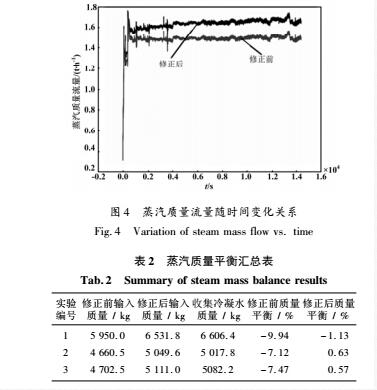
对图4中蒸汽质量流量数值进行时间积分,可获得对应条件下的蒸汽输入总质量。实验完成,冷却后通过实验壳下端收集称重装置称量获得输出的冷凝水的总质量,通过对比两者差异来评价修正前后质量流量计测量的精度。结果如表2所示,实验编号1为图4中所示质量结果统计,编号2和3为另外两次测试结果。质量平衡结果表明,修正之后的质量流量计公式可以明显提高测量精度。
5、结束语
针对工作状态发生变化的质量流量计工作环境,分析可能影响因素,并根据不同稳态设计结果拟合获得适合非稳定状态下的流量计修正计算公式,结论如下:(1)当实际运行工况与设计条件发生偏离时,孔板流量计的测量准确性会降低;(2)蒸汽质量流量测量时,蒸汽的膨胀性系数对测量结果影响很大;
(3)质量平衡结果表明,修正后的孔板流量计,可以适用于变工况条件的蒸汽测量,计算精度有了明显提高。